It’s a proven fact, when we install a CleanScrape® Cleaner at a plant they always want more. Try it risk-free, and you will too!
You will love the CleanScrape® Cleaner because it:
- Will last up to four times as long as traditional cleaner systems - Click here to find out how much longer it will last in your exact situation.
- Is easy to install with little ongoing maintenance needed, requiring only one tensioner adjustment - EVER!
- Offers the lowest blade-to-belt pressure of any cleaner on the market.
- Safe for use on even mechanically spliced belts, unlike other tungsten tipped pre-cleaners.
- You can put it anywhere! Installed at an angle, the CleanScrape® Cleaner requires very little space for installation.
- Works well with dry, wet or sticky materials, making it perfectly suited for aggregate, limestone, cement or coal.
The Bottom Line
The CleanScrape® Cleaner is an innovative, durable metal-tipped belt cleaner that provides maximum cleaning efficiency without compromising your belt.
You can use the CleanScrape® Cleaner with both mechanical and vulcanized splices because of its durable tungsten carbide tips, which are available in multiple grades of carbide to match your application.
Ask us about trying it Risk-Free ASAP!
If you don’t think it’s the best cleaner you’ve ever used, we will give you your money back. Period.
Our technicians and engineers are available to provide expert advice and assistance on this product and all of your bulk material handling questions and problems. Please contact us today and let us help!
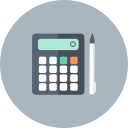
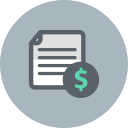
- CleanScrape® Belt Cleaner - Demonstration
- Cleanscrape® Belt Cleaner Handles Bed Ash at a Coal-Fired Power Plant
- Cleanscrape® Belt Cleaner Handles Copper Ore
- Cleanscrape® Belt Cleaner Handles Crushed Glass
- Cleanscrape® Belt Cleaner - Hardrock Applications
- Cleanscrape® Belt Cleaner - Overview
- Cleanscrape® Belt Cleaner - Cleaning Performance
- Cleanscrape® Belt Cleaner - Installation
- Cleanscrape® Belt Cleaner - Mechanical Splice Tests
CleanScrape® Cleaner Eliminates Extensive Carryback On Conveyors Carrying Slag
CleanScrape® Cleaner Eliminates Excessive Carryback on Conveyor Carrying Wood Chips
New Belt Cleaner Saves 24 Hours Per Week In Cleanup Time
CleanScrape® Cleaner Improves Operations At Coal-Fired Power Plant
CleanScrape® Cleaner Improves Operations At Rock Quarry
Chute Clogging And Spillage Corrected With CleanScrape® Cleaner
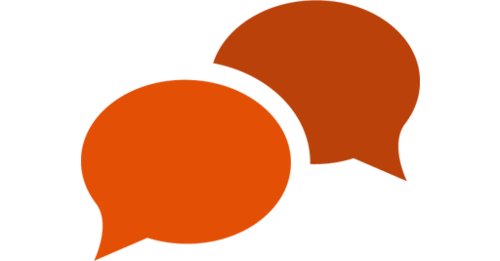
What Our Customers Are Saying...
"We have employees of 30+ years of whom rave about these cleaners, saying they are the best thing seen at Ulan since they started!"
Robert Thraves, Outbye Services Superintendent, Ulan Underground Coal Mine Read More Testimonials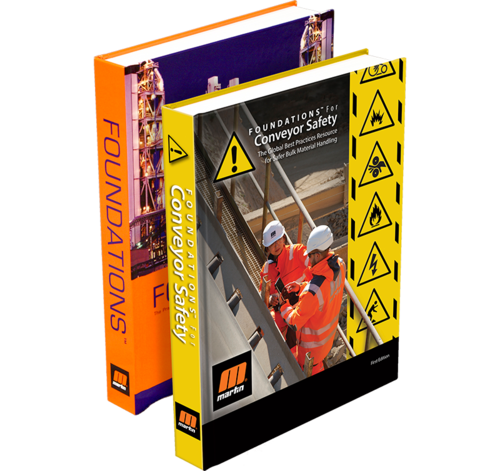
Foundations™ for Conveyor Safety
Learn to Calculate your Return on Conveyor Safety™ with our compilation of worldwide best practices for safer bulk material handling in this first-ever textbook dedicated exclusively to the safety of conveyor systems.
Request Your FREE PDF or Hard-Back Copy