Slider Cradle
Installed under the skirtboard of a transfer point, Martin® Slider Cradles support the edges of the belt to eliminate sag. These cradles prevent transfer point spillage by stabilizing the belt’s path and allow the effective sealing of the belt edge. Cradles are available with high-performance UHMW or Stainless Steel Bars to match application requirements.
Features and Benefits:
- The Martin® Slider Cradle supports the belt edges, allowing an effective seal
- Slider Cradle eliminates pinch points where trapped material can gouge the belt
- Conveyor belt glides over UHMW bars without heat buildup
- Use both top and bottom of unique "box bar" to provide dual-wear surfaces for double wear life
- Slider Cradle adjusts for wear easily with simple tools
- Fits any troughing angle. One bar per side for belts 18 (457 mm) to 42 inches (1067 mm); wider belts require two bars per side. Center bar or rollers may be required.
- Protected by U.S. Patent No. 4,898,272
Our technicians and engineers are available to provide expert advice and assistance on this product and all of your bulk material handling questions and problems. Please contact us today and let us help!
Filtrating Dust At Environmentally-Conscious Coal-Fired Power Plant
Belt Support System Allows For 24/7 Operating Schedule
Installing Dust Containment Solutions at Sugar Processing Plant
MartinPLUS® Installation Services Redesign Power Plant Transfer Points
Transfer Point Solutions Solve Fugitive Cargo Issues
Martin Products Help World's Highest Production Coal-Fired Power Plant
Salt Buildup At Chemical Plant Causing Frequent Shutdowns
Belt Support Products Solve Fugitive Dust And Spillage Problems
Martin Engineering Offers Dependable Solutions When Others Fail
Martin Provides Effective Belt Support Solution
Transfer Point Solutions Result In Safer, More Productive Coal Mining
Cement Plant Needed Transfer Point Solutions
Transfer Point Products Improve Severe Spillage And Dust Problems
Spillage Problems Corrected By Transfer Point Redesign
Power Plant Needs Cleaner, Safer, More Productive Material Handling System
Transfer Point Solutions Resolve Carryback At Kentucky Energy Plant
Martin Transfer Point Solution Saves Mainframe
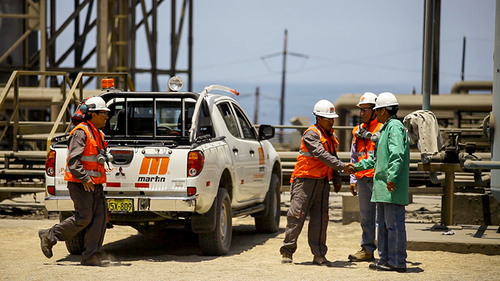
Free Engineering and Application Assistance
Our technicians have solved problems for people in your industry all over the world. Take advantage of our wealth of knowledge. Tell us about your situation today to learn how Martin can improve your performance, safety and bottom line - with no obligation. We want to ensure that you choose the right solution for your exact needs and we are willing to invest the time upfront to get it right the first time.
Briefly Describe Your Application